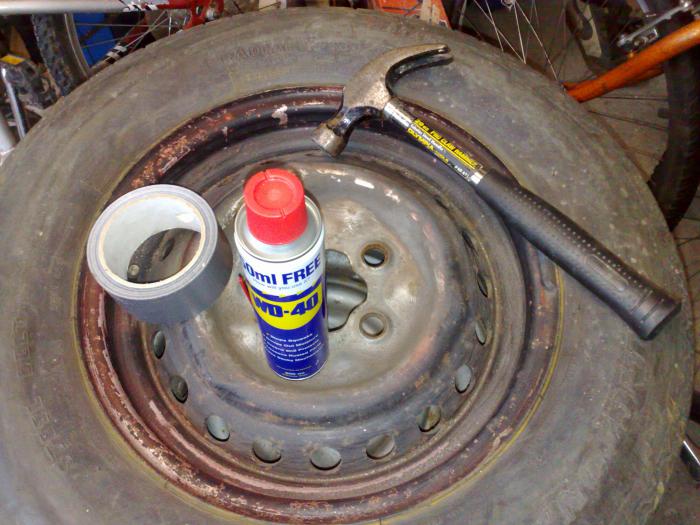
A few days before christmas we headed off on the first long trip in Rocky since buying him. The cross-country trip from our home town of Bristol to my parent’s house in Cambridgeshire is always a slog, rarely less than four hours, but with an early start to beat the traffic, we were on the M5 heading north before 7am. Despite the driving wind and rain, the van did really well. With the under-powered but frugal 1.6 diesel “CS” engine we were mostly able to keep it at a steady 60 mph, only slowing down on the inclines where there is usually a crawler lane. Future plans for the van include changing the engine for a slightly more powerful 1.9 “1Y” diesel engine (from an old golf or caddy), which won’t make it much faster, but apparently wth 29% more torque should help us keep up with the trucks on the hills.
I had been nervously excited for days about doing this trip – the van was fully loaded with food and drink for xmas, bedding for camping over new year and xmas presents, so we needed to make it to our holiday cottage in Norfolk. About a week previously we had decided to upgrade our breakdown cover to include “relay”, meaning we were guaranteed to at least be towed to our destination if it couldn’t be fixed by the roadside.
Up until now we had only done fairly short trips e.g. 60 miles and every time so far something had cropped up, notably indicators and dash light not working on one trip (on Jo’s first stint behind the wheel), and windscreen wipers suddenly stopping working. Each time something like this happens, a small amount of panic and dread creeps in – panic that you won’t make it home, and dread that sorting it out is going to lead to expensive auto-electrician bills. However, in both these cases I managed to find and fix the fault with no external help.
For the record, the indicators and dash light issue was caused by an earth wire coming loose behind the glove box – once reattached to the earth crown, the problem went away, and the windscreen wiper issue was caused by a blown fuse. The wipers share a fuse with the blower motor circuit and I already knew the blower motor was on its way out as it was squeaking badly and varied in speed, so when that seized the fuse blew. The advice found on club 80 90 is to separate the blower and wiper onto different fuses, which I will do in due course. I also need to replace the blower motor, which involves removing the dash (which in return requires removing the steering column – or at least removing the driver seat and detaching the steering column).
So on the day of our 200 mile cross-country trip, we set off early in the dark to beat the holiday traffic, and found ourselves on the motorway in driving rain and wind. Despite requiring some serious concentration to keep it in the correct lane, Rocky made it to Wisbech with no problems, other than the heating stopping for the last hour or so – probably the result of air locks in the cooling system. Triumphantly pulling onto my parents driveway I felt instantly more relaxed about the prospect of future long journeys in Rocky.
In the morning I checked the oil and topped up the coolant, reloaded all the luggage and we waved goodbye to my parents to set off on the next leg of the trip… before sitting on the driveway in quiet despair as the van wouldn’t start. Turning the key, the ignition lights came on, but nothing happened when you tried to turn it over. If the battery was flat you might expect some dimming of the ignition lights or at least the sound of the starter trying, but failing, to turn the engine, but all I could hear was a click of a relay somewhere. We tried charging the battery for a bit and jump starting it from a portable jump start pack, to no avail. There must therefore be a problem with the starter motor, or associated electrics. After fumbling around looking for loose connections but finding nothing, I swallowed my pride and called the AA.
While we were waiting for the AA to turn up (at least drinking a cup of tea in the comfort of my parents living room rather than by the side of a rainy motorway or A-road), I was feeling quite despondent. I knew there was nothing major wrong with van, but I hated the idea that as it was a couple of days before xmas, it would be virtually impossible to get hold of any parts and get them fitted in time for the start of our holiday, so might be faced with a dead van that could only be bump started (and that’s not the simplest thing in a two-tonne vehicle!). I’ve always liked to think of myself as mechanically minded, and have worked on cars myself in the past, including helping to build a Citroen 2CV from spare parts. However, in more recent years, electrical problems i’ve had on more modern cars have usually boiled down to “Computer sais no.”, followed by expensive diagnostics at a specialist garage. I wondered how I would deal with this type of problem stuck by the side of a foreign motorway. My spirits were lifted when the AA mechanic talked me through his simple diagnostic procedure and found a way to get us back on the road.
The AA mechanic attached a wire to the spade connector on the starter solenoid with a bullet connector on the other end. With the ignition switched on, this bullet connector is pressed for a second or two on the positive terminal of the battery and the engine turns over and starts. This simple, slightly inconvenient method of starting the van is how we carried on with our trip without having to resort to bump starting or finding an auto-electrician. As well as solving our immediate dilemma, this has also changed my perception of the engine – it has reminded me that Rocky has an incredibly simple engine with no ECU or immobiliser to worry about, so it should be within my capabilities to diagnose the problem and fix it myself when we are back in Bristol.
I’ve since done a bit of reading about starter solenoids, and I now understand that a solenoid is a type of relay – the 12 volt feed that I am providing via the workaround is not powering the starter motor, but causing the solenoid to complete a circuit on the thicker wires needed to handle the heavy current that the starter motor needs. This makes sense and is a bit of a relief as I initially thought that I was man-handling the much higher current needed by the starter and was surprised that the wire hadn’t melted!
The next week or so was spent hibernating in a holiday cottage and so we didn’t use Rocky much, but when we did it involved running round the back, removing whatever was obscuring the engine bay lid, removing the lid, finding the ignition hack wire and touching the end on the battery terminal. I got a few weird looks, particularly on our last day at the cottage, starting from cold, the engine can smoke a bit for the first few minutes, until the engine gets up to temperature (I need to get the glow plugs replaced as it only fires on a couple of cylinders in the cold until it warms up, which leads to lots of unburnt fuel coming through the exhaust). Our holiday cottage neighbours (them with their two shiny black Range Rovers, us with a scruffy white campervan touched up with splodges of grey primer), were loading their luggage at the same time as us, and I needed to start the engine before we loaded everything into the back. As it idled, the wind direction and a particularly smoky start conspired to fog them back indoors until we were gone!
Our next stop was with friends/ relatives in Derbyshire where we camped for a couple of nights on their driveway with the luxury of electric hookup. This was fairly vital as I have yet to get our propex heater serviced and working, so we were relying on an electric fan heater to keep the van warm. In exchange for me sorting out their wifi network, Paul (who just happens to be a very good mechanic with a garage full of tools and random spares), diagnosed the ignition problem as being a relay, which had probably got thoroughly soaked in rainwater/roadsplash on the first leg of the trip and stopped supplying sufficient voltage to the starter solenoid. As luck would have it, he had a spare, which he fitted, and secured with a cable tie to the bulkhead with the connectors pointing downwards so any road splash will drain away rather than soak in.
Rocky got us back to Bristol again with no more issues, and no problems since. I also started putting together an electrical toolkit to carry around in Rocky, and came across some electrical spares that I used to carry around in my old T25 – including, of course, a spare relay!